
Note: IronCAD can export in many file formats depending on your geometry. Tip: Curves’ accuracy ratio: The higher the setting, the smoother the surface will be when dealing with complex geometries, especially if surfaces contain sudden small changes with small radii (like the bumps on a golf ball).
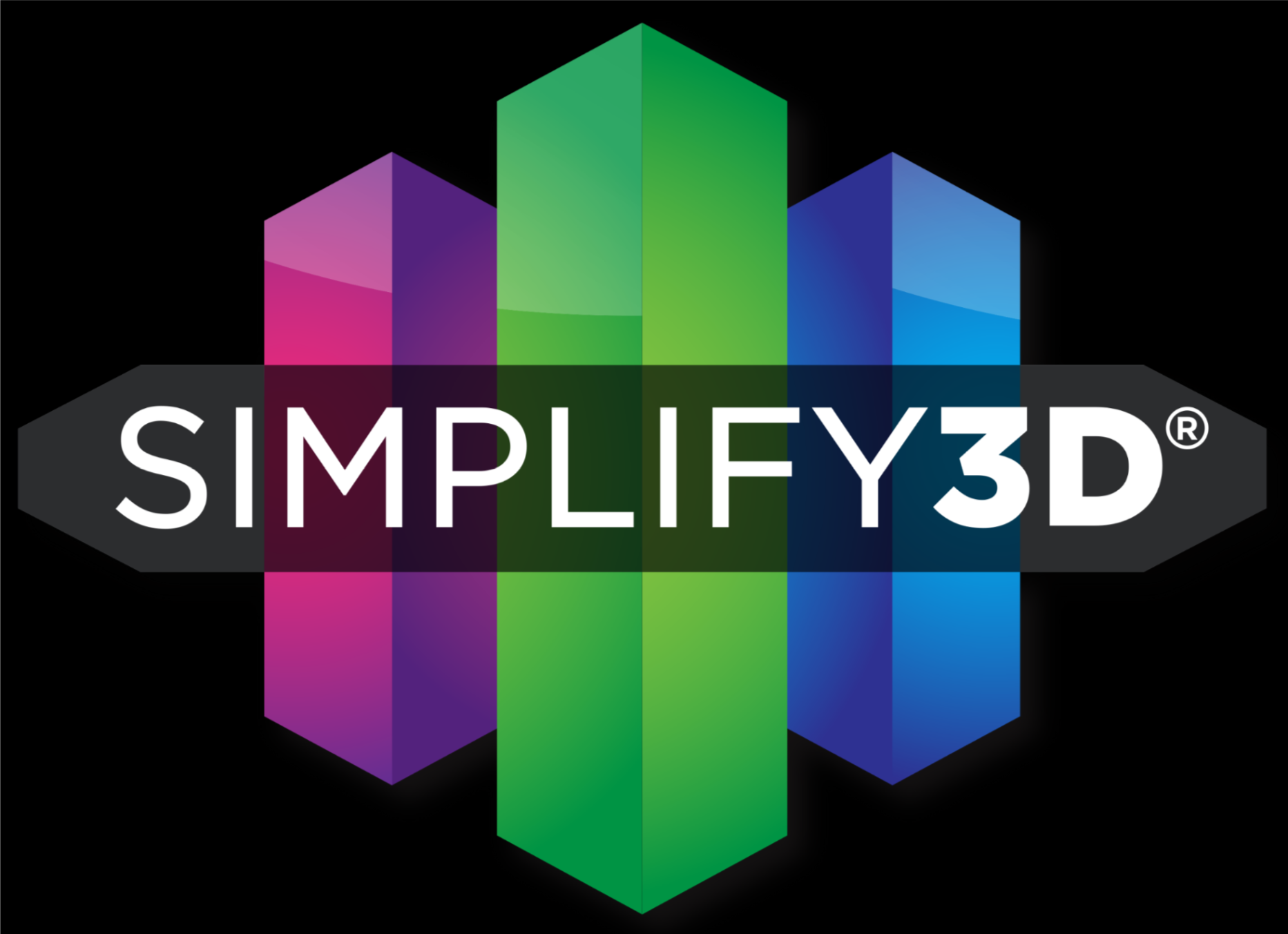
Select Tools > Generate CATPart from Product.The new part is now ready to be exported as an STL file.Copy each of the individual components from the working files and paste them into the new combined model file (the geometries of all of the parts should retain and align correctly in the combined part).Once you have the assembly completely separate into individual components, select File > New Part.Repeat steps and until you have copied all of the components and pasted them as individual parts.Paste the component in a new part window.Select one component from your master CATProduct File and copy it.Select File > New > Part > Name the new part.File Menu > Open > select your source file (assemblies import as CATProduct).Saving CATProduct files as CATPart Files for 3D printing: The procedure described below is one of several methods for doing this. To create an STL file from it, you must first convert it to a multi-bodied part.

If the source design was saved as an assembly, it is imported to CATIA as a CATProduct. STEP or IGES), must be saved as CATParts. Therefore, source files, including those saved in a neutral format (i.e. Note: CATIA V5 is capable of creating STL files from CATPart files, but not from assemblies (CATProduct files) or geometrical representations (car files).

Select STL command (we recommend setting maximum segmentation to 0.015 mm).You can also just load your native CAD into our online quoting tool to get instant pricing!
